Золоудаление
Система золоудаления котла
При сжигании твердого топлива зола и частично недогоревшее топливо выпадают в топочном устройстве, газоходах, золоуловителе и уносятся в дымовую трубу. Все осаждающиеся в пределах котельного агрегата твердые частицы принято делить на две части - шлак и золу. Доля шлака и золы от общего содержания минеральной части в топливе зависит от способа сжигания твердого топлива.
Вид топочного устройства | Доля золы топлива, % | |
---|---|---|
В шлаке | В золе | |
Слоевая топка с ручным забросом или с ПМЗ | 80 - 90 | 10 - 20 |
Слоевые цепные решетки для угля | 75 - 90 | 10 - 25 |
Камерные топки с молотковыми мельницами и мельницами-вентиляторами | 5 - 15 | 85 - 95 |
То же с среднеходными и другими мельницами | 5 - 10 | 90 - 95 |
Ориентировочные значения распределения зольности топлива даны в табл. 7- 4, где большие значения а3 даны для топок без возврата уноса.
Таблица 7-4. Распределение зольности топлива на шлак и золу
По данным теплового расчета и табл. 7-4 масса шлака, кг/с (кг/ч) и массы золы кг/с (кг/ч).
Полученные расчетом величины и Gшл и Gз позволяют выбрать систему шлакозолоудаления. Если Gшл+G3 меньше 0,06 кг/с (200 кг/ч), то допускается ручное удаление шлака, при большем количестве золоудаление обязательно следует механизировать. При количестве шлака и золы до 1,1 кг/с (4000 кг/ч) обычно применяются периодически действующие механизмы; для количества шлака и золы до 2,2 кг/с (8000 кг/ч) - непрерывно действующие, и если оно превышает 3,3 кг/с (12 000 кг/ч), необходимы постоянно действующие устройства с резервированием наименее надежных узлов.
Золоудаление в котельных
В производственно-отопительных котельных применяют следующие устройства для удаления шлака и золы.
Ручное золоудаление
При ручном удалении - узкоколейные вагонетки с опрокидывающимся кузовом (рис. 7-28). Вагонетки этого типа могут перемещаться по рельсам или иметь на колесах резиновые обода и двигаться по обычному полу иногда с помощью механизмов. Шлак и зола перевозятся сухими.
Рис. 7-28. Опрокидывающаяся вагонетка узкой колеи. 1- кузов; 2 - рама; 3 - накладки для фиксации положения кузова.
Механизированное золоудаление
При механизированном удалении могут быть применены скиповые и другие подъемники, скреперные установки, скребковые конвейеры, шнеки и некоторые другие устройства. К постоянно действующим устройствам относится гидравлическая система золошлакоудаления с багерными насосами и аппаратами Москалькова.
В некоторых случаях находит применение золоудаление, выполняемая как всасывающая или напорная.
Выбор системы золоудаление
Выбор системы удаления шлака и золы зависит от экономических показателей системы и последующего использования золы и шлака. Для золы некоторых топлив, например эстонских сланцев, назаровских бурых углей, в золе которых содержится более 20% СаО и которые можно использовать как вяжущие материалы, увлажнение недопустимо.
Из шлаков топочных устройств, находящихся в воде в раздробленном состоянии, можно отделить некоторое количество несгоревших частиц топлива и этим улучшить их качество как наполнителя.
При выборе производительности механизированной системы удаления шлака необходимо учитывать запас для перерывов в работе на несколько часов.
На рис. 5-54,а было показано устройство для размещения вагонеток под котлом, их передвижение на отвал может быть осуществлено с помощью механической тяги - лебедкой, автомотриссой или другим способом. Однако применение вагонеток любого типа не исключает ручной труд.
Периодическое механизированное удаление шлакоудаление в сухом и мокром виде может быть осуществлено с помощью скреперной установки.
Устройство скреперной установки
Шлак и зола (рис. 7-29) из бункеров котлов 1 через затворы спускается в специальный железобетонный канал 2, по которому перемещается ковш скрепера 3 емкостью до 0,5 м3. Для перемещения ковша служат стальные канаты 4 и лебедка с реверсивным ходом 5, установленная в помещении котельной. Заполненный ковш по эстакаде 6 (имеющей наклон около 30°) перемещается канатом 4 к установленному вне котельной бункеру 7 и, опрокидываясь, опорожняется. Для направления хода каната служат ролики 8; в натянутом состоянии канат поддерживается с помощью натяжного устройства 9. Лебедка имеет электродвигатель мощностью 11 кВт, конечные выключатели и пульт управления. Канал, по которому перемещается скрепер, выполняется шириной 1,25 м и с разной глубиной. В канале предусматриваются приямки или параллельный ему коридор.
Рис. 7-29. Скреперная установка для удаления шлака и золы в мокром или сухом виде
Шлак и зола, периодически удаляемые из котлов, накапливаются при сухом шлакоудалении за сутки и за 8 ч при мокром в бункере 7, который обычно утепляется. Скорость перемещения скрепера составляет 0,5 м/с, что в зависимости от емкости ковша и длины пути его перемещения позволяет удалить из котельной от 0,0005 до 0,0013 м3/с (от 2 до 5 м3/ч) шлака и золы или от 0,8 до 2,0 кг/с (от 3 до 7 т/ч), если считать по массе.
Вместо ковша скрепера в подобных системах иногда применяют металлический ящик-тележку с отверстиями в дне и стенках для стока воды, перемещающийся на колесах по стальным направляющим в бункер. Схема установки скрепера с тележкой подобна показанной на рис. 7-29. Расчет производительности скреперной установки, кг/с, можно произвести по следующей формуле:
В формуле:
vк - емкость ковша, м3;
qн - насыпная масса шлака и золы при удалении;
kзапол - коэффициент заполнения ковша, принимаемый равным 0,9 для наклонных и 1,25 для горизонтальных участков;
L - длина пути ксмвша, м (нагруженного и порожнего);
wр wx - рабочая скорость движения ковша около 0,5 м/с и холостая - около 1,0 м/с;
10 - время, с, на перерывы движения ковша для переключения хода.
Для возможности периодического ремонта производительность скреперной установки должна быть больше в 2 - 3 раза максимального выхода шлака и золы из котельной.
Пневматические системы золоудаление
Пневматические системы золоудаления могут работать как всасывающие или нагнетающие: первые применяют в тех случаях, когда расстояние от котельной до осадительной или разгрузочной установки не более 200 м, вторые - до 600 м (при сухом использовании шлака и золы).
Общая схема пневматической системы золоудаление из котельной показана на рис. 7-30. Шлак с температурой до 600°С из бункеров 1 топочного устройства через затворы 2 поступает в трехвалковую шлаковую дробилку 3, где измельчается до 20 - 25 мм. Далее шлак попадает во всасывающую насадку 4 (рис. 7-31,а). Насадка состоит из кармана а, внутренней трубы б, поворачивающейся на своей оси и меняющей размеры входного отверстия из кармана в трубопровод шлака и воздуха с помощью рукоятки в и барашка а. Смесь воздуха и шлака, как показано на рис. 7-30, с концентрацией 4 - 8 кг шлака и золы/кг воздуха, со скоростью 22 - 25 м/с через отключающий пробковый кран 5 (одна из конструкций которого дана на рис. 7-31,б) по золопроводу 10 направляется в циклон-осадитель 11. Из него воздух с неуловленной в циклоне 11 пылью поступает в следующий циклон 13, и затем воздух через эжектор 14 сбрасывается в дымовую трубу.
После удаления шлака краном 5 и затворами 2 часть трубопроводов и бункера для шлака отключаются от системы. Затем к системе подключают бункера с золой 6 с помощью затворов 7 к насадке 4 через течку 8 к тому же золопроводу 10 и к циклону 11.
Иногда золу можно транспортировать прямо из бункера через телескопического типа насадку 9. Из циклонов 11 и 13 через затворы 12 шлак и зола ссыпаются в бункер 16, а из последнего перйодически через затвор 17 загружаются в вагоны или в автомашины; при необходимости шлак и золу увлажняют после бункера.
Для работы системы требуется разрежение в 36 - 40 кПа (0,36 - 0,4 кгс/см2), которое может быть создано с помощью многосопловых эжекторов или водокольцевого вакуум-насоса.
На рис. 7-30 показана схема с паровыми эжекторами 14, получающими пар давлением 1-1,3 МПа (10 - 14 кгс/см2) через вентиль 15. Для отключения участков системы необходимы пробковые краны 5 (одна из конструкций которых показана на рис. 7-31,б). Наиболее изнашиваемыми участками трубопроводов являются колена; их целесообразно выполнять чугунными с закладкой в сильно изнашиваемых местах меняемых вставок 1, например, из плавленого базальта, как это изображено на рис. 7-31,в. Трубопроводы для шлака и золы рекомендуется выполнять одинарными с минимальными внутренними диаметрами для транспорта шлака 125 мм и для золы 100 мм и толщиной стенки порядка 10 - 14 мм.
В напорных системах используются двухкамерные или винтовые насосы и компрессоры. Для крупных котельных с выходом шлака и золы 4 - 5 кг/с (15 - 20 т/ч) по нормам проектирования электростанций необходимо резервировать пневматическую систему гидравлической.
Рис. 7-30. Общая схема пневматической системы удаления шлака и золы
Рис. 7-31. Пример выполнения загрузочной насадки (а), отключающего пробкового крана (б), колена шлакозолопровода (в) пневматической системы удаления шлака и золы.
Наиболее часто применяется установка, в которой эоловая и шлаковая пульпы перекачиваются из котельной на золоотвал грунтовым - песковыми и багерными насосами.
Гидравлическое золошлакоудаление
Принципиальная схема гидравлического золошлакоудаления показана на рис. 7-32. Из шахт под котлами 1 шлак смывается соплом на решетку и в канал 8. Крупные куски шлака дробятся до размера порядка 100 мм. Канал (рис. 7-33) выполняется из железобетона и выкладывается плитами из базальтового литья для защиты от износа. Канал имеет уклон от 0,015 до 0,02.
По пути движения смеси шлака с водой для предупреждения отложений установлены сопла 10, называемые побудительными. Из канала 8 самотеком пульпа попадает в металлоуловитель 4 и далее поступает в дробилку для шлака 5 для измельчения его до 20 мм и далее в багерный насос 6, которым она и перекачивается на золоотвал.
Из золоуловителей 2 через золосмывной аппарат зола смывается в канал 9, который в местах возможного выпадения золы также оборудован побудительными соплами 10. Затем через металлоуловитель 4 зола Песковым насосом 7 подается в золопровод, иногда зола собирается в емкости 3.
Далее путь золы таков же, что и у шлака.
Для смыва и работы сопл устанавливаются центробежные насосы смывной воды 11, забираемой из бака технической воды 12. На некоторых установках вместо багерных и песковых насосов установлены аппараты Москалькова, состоящие из приемной камеры для пульпы, сопла и диффузора. Струя воды из сопла с давлением 6,5 МПа (25 - 65 кгс/см2) подхватывает шлакозоловую смесь и гонит ее через диффузор в золопровод, который изготовляется из стальных труб. Насосы 6 консольного типа имеют одно рабочее колесо, выполненное из износоустойчивых сплавов, и броню для корпуса; насосы создают напор в 0,45 - 0,5 МПа (4,5 - 5 кгс/см2), частота вращения колеса от 585 до 1480 об/мин.
Смывные насосы подают к соплам чистую воду и должны иметь напор 1 МПа (10 кгс/см2). Для смыва шлака требуется у сопл давление не ниже 0,5 МПа (5 кгс/см2), а работа побудительных сопл успешна лишь при давлении воды перед соплом около 0,7 МПа (7 кгс/см2). Скорость воды в каналах для шлака должна быть не ниже 1,6 м/с, золы -1,0 м/с. Побудительные сопла устанавливаются по оси канала на высоте 150 - 250 мм от дна и с наклоном к последнему. Стальные трубы для золошлакопроводов выбираются с толщиной стенки до 12 мм, диаметром 250 - 400 мм и укладываются над землей на опорах. Скорость движения шлакозоловой смеси с водой принимается в пределах 1,6 - 2,0 м/с, причем до начала и после окончания откачки пульпы золошлакопровод должен быть промыт чистой водой и дренирован.
Рис. 7-32. Принципиальная схема гидравлического удаления шлака и золы из котельной
Рис. 7-33. Схема смыва шлака и золы для их удаления по каналу.
1- базальтовые плиты для защиты канала с формой А, Б, В.
Для удлинения срока службы золошлакопровод через каждые 1 - 2 года поворачивают вокруг оси на угол 45 - 60° и заваривают изношенные участки. Места для отвала шлака и золы выбираются в оврагах, на склонах холмов и на подобных территориях, позволяющих обеспечить работу котельной в течение 25 лет, а при использовании шлака и золы в качестве сырья и раздельном их складировании - на 3 года.
Таб. 7-5. Ориентировачные технико-экономические показатели системы золоудаление
Вода после золоотвала до попадания в водоемы должна быть осветлена и нейтрализована до норм, установленных Госсанинспекцией. Для предварительной оценки при выборе системы золоудаления можно воспользоваться табл. 7-5 с ориентировочными технико-экономическими показателями.
Для того чтобы купить золоудаление вы можете оформить заявку в отделе сбыта по телефону +7 (7172) 69-59-73 или оформить заявку он-лайн.
Статьи
Документы завода
Собственное производство
- Паровые котлы от 300 кг до 2.5 тонны пара в час
- Промышленные водогрейные котлы от 150 КВт до 4 МВт на всех видах топлива
- Механические топки ТШПМ, шурующая планка и ТЛПХ, ленточное полотно прямого хода
- Циклоны для очистки воздуха и дымовых газов для производств и промышленных отраслей
- Транспортеры и системы топливоподачи и шлакоудаления
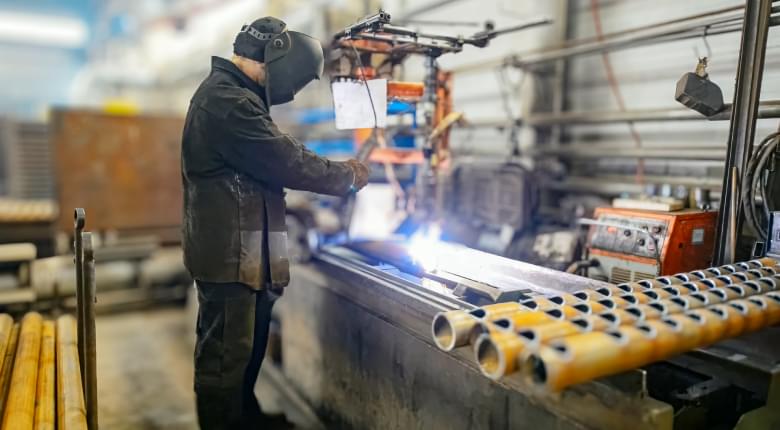
с производства
Мы на
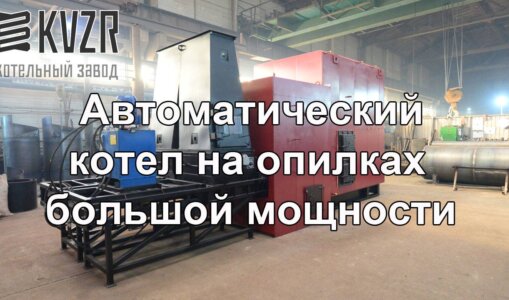
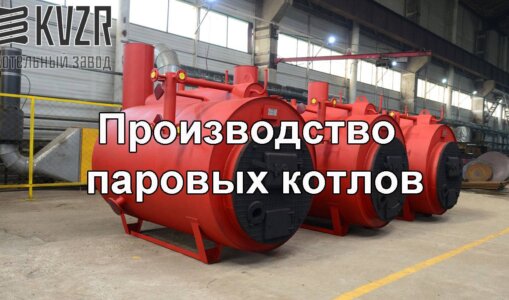
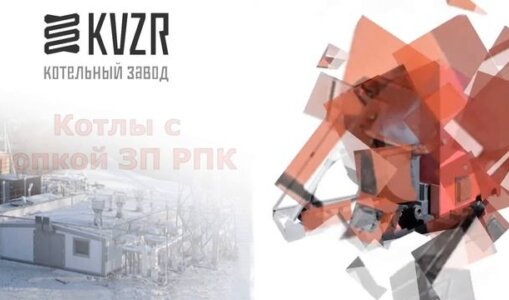
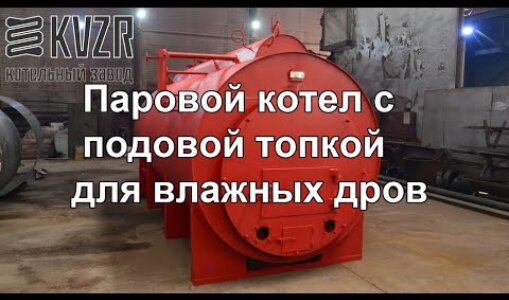
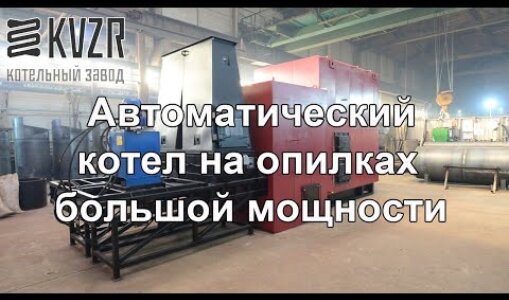
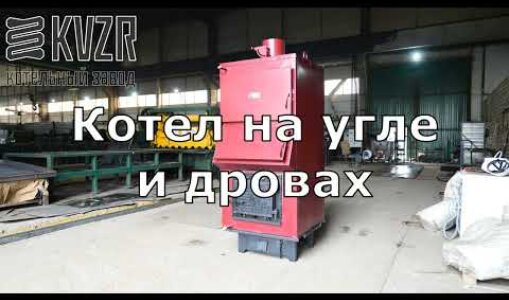